What is Modal Analysis?
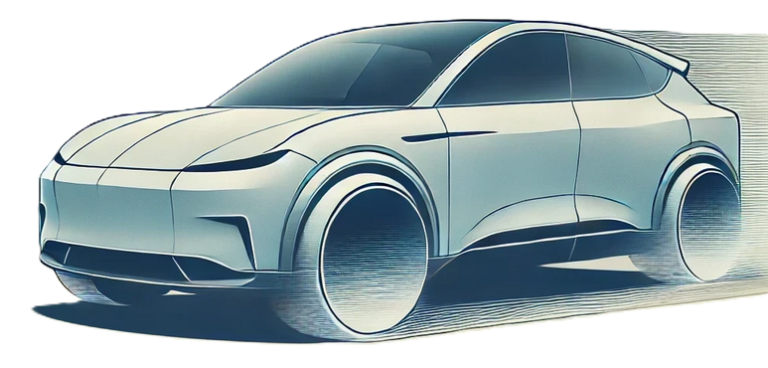
By: S. Meszaros – 2025.03.18
Introduction:
Why Vibrations Matter (And Why Ignoring Them Is a Bad Idea)
Vibrations. They’re everywhere. In the engine of a car, in the structures of a bridge, the quiet tremor of a skyscraper resisting the wind. Sometimes they’re harmless, other times, they’re silent saboteurs—shaking apart machinery, cracking structures, and, in extreme cases, bringing down entire bridges in a spectacular act of self-destruction.
That’s where modal analysis comes in—the engineer’s secret weapon in the war against unwanted motion. It’s the science of understanding how objects naturally vibrate when disturbed, like plucking a guitar string and hearing its unique tone. Except, in this case, it’s not about music—it’s about ensuring the safety, efficiency, and longevity of everything from aircraft wings to wind turbines.
The world of engineering is full of cautionary tales—structures that failed because someone underestimated the power of resonance. The Tacoma Narrows Bridge, which twisted and collapsed in 1940 due to wind-induced oscillations, is just one example. The stakes are just as high in the aerospace industry, where an aircraft wing vibrating uncontrollably at high speeds could lead to disaster. In automotive design, a poorly tuned chassis can result in annoying rattles or, worse, a ride so uncomfortable it makes the driver feel like they’re going to throw up.

What You’ll Discover Here:
🔹 What modal analysis is—and why it’s important in engineering
🔹 The core concepts—natural frequencies, mode shapes, and damping, explained without the fluff.
🔹 How engineers perform modal analysis—from hammer tests in real-world labs to powerful Finite Element Analysis (FEA) simulations.
🔹 Real-world applications—how industries like automotive, aerospace, civil engineering, and energy rely on it to stay ahead.
🔹 Common challenges—and how engineers tackle them to prevent disasters.
Understanding Modal Analysis: The Science of Structural Rhythm
Every structure, from the smartphone in your hand to the bridges that stretch across rivers, has a hidden rhythm—a unique way it vibrates when disturbed. This vibrational behavior isn’t random or accidental; it’s as much a physical property of an object as its color, weight, or length. Just like a bridge has a fixed span or a car has a defined weight, every structure has inherent vibrational characteristics that dictate how it moves when energy is introduced.
What is Modal Analysis?
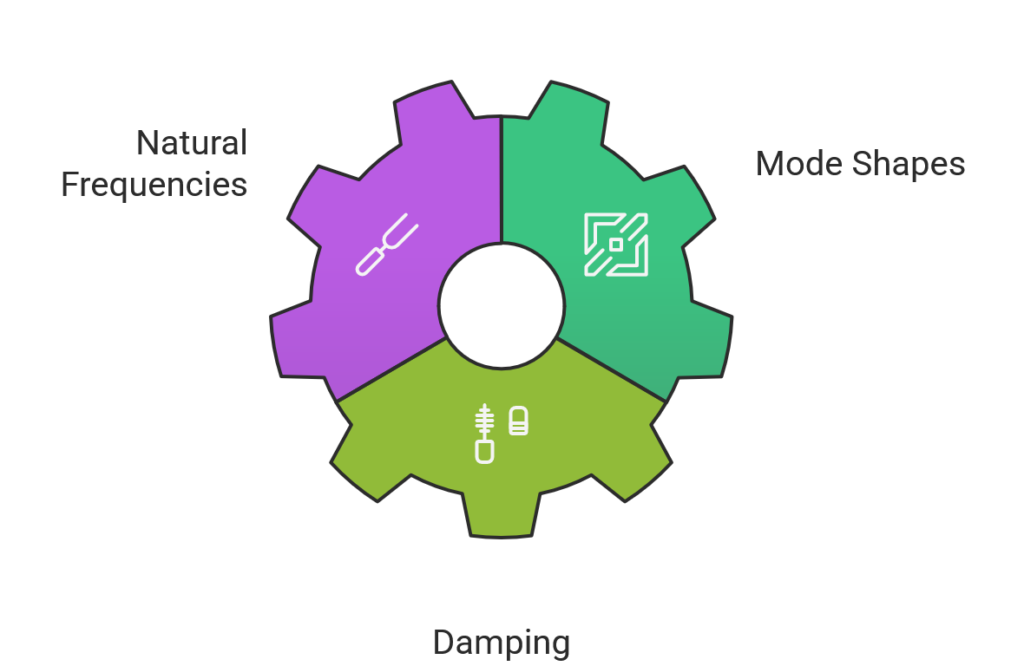
At its core, modal analysis is the study of a structure’s natural vibration characteristics. It helps engineers break down complex motion into simple components—natural frequencies, mode shapes, and damping properties—to understand exactly how an object moves when subjected to external forces.
Think of it this way: Imagine striking a tuning fork. The fork doesn’t just vibrate randomly—it oscillates in a very specific pattern at a distinct frequency. That’s its natural frequency, the point at which it prefers to vibrate. Similarly, if you were to tap a bridge (with some beef of course), a turbine blade, or an aircraft wing, each would have distinct vibration modes—some bending, some twisting, some oscillating at different speeds.
But here’s the key takeaway: These vibration characteristics are a fundamental property of the object itself. Just as a metal beam has a fixed weight and density, it also has fixed natural frequencies and mode shapes. They don’t change unless the structure is physically altered—by adding mass, changing material, or modifying its shape.
The Modal Properties
1️⃣ Natural Frequencies – The frequencies at which a structure naturally wants to vibrate. At these points, even small external forces can create large oscillations, leading to potential resonance issues (which, in extreme cases, can cause structural failure).
2️⃣ Mode Shapes – The specific ways in which a structure deforms when vibrating at its natural frequencies. Different parts of the structure move in unique patterns—some bending, some twisting, some remaining stationary at “nodes.” These mode shapes help engineers understand which regions are most affected by vibrations.
3️⃣ Damping – The energy dissipation mechanism that reduces vibration over time. Without proper damping, a system could vibrate indefinitely, leading to fatigue and potential failure. Effective damping is key in applications like automotive suspensions (to ensure a smooth ride) and aerospace structures (to prevent unwanted oscillations during flight).
Together, these three factors—natural frequency, mode shape, and damping—define a structure’s modal model, providing a complete picture of how it behaves dynamically.
Why Do Engineers Care About Vibrations?
Vibrations are an unavoidable part of the physical world. Most structures experiences some level of oscillation due to external forces like wind, mechanical loads, temperature changes, or human activity. But if not carefully managed, vibrations can become a serious problem.
🔹 Safety First – Preventing catastrophic failures due to resonance. The infamous Tacoma Narrows Bridge collapse (1940) is a textbook example—where undamped oscillations amplified by the wind caused the entire bridge to self-destruct. Modal analysis ensures structures are designed to avoid such resonance disasters.
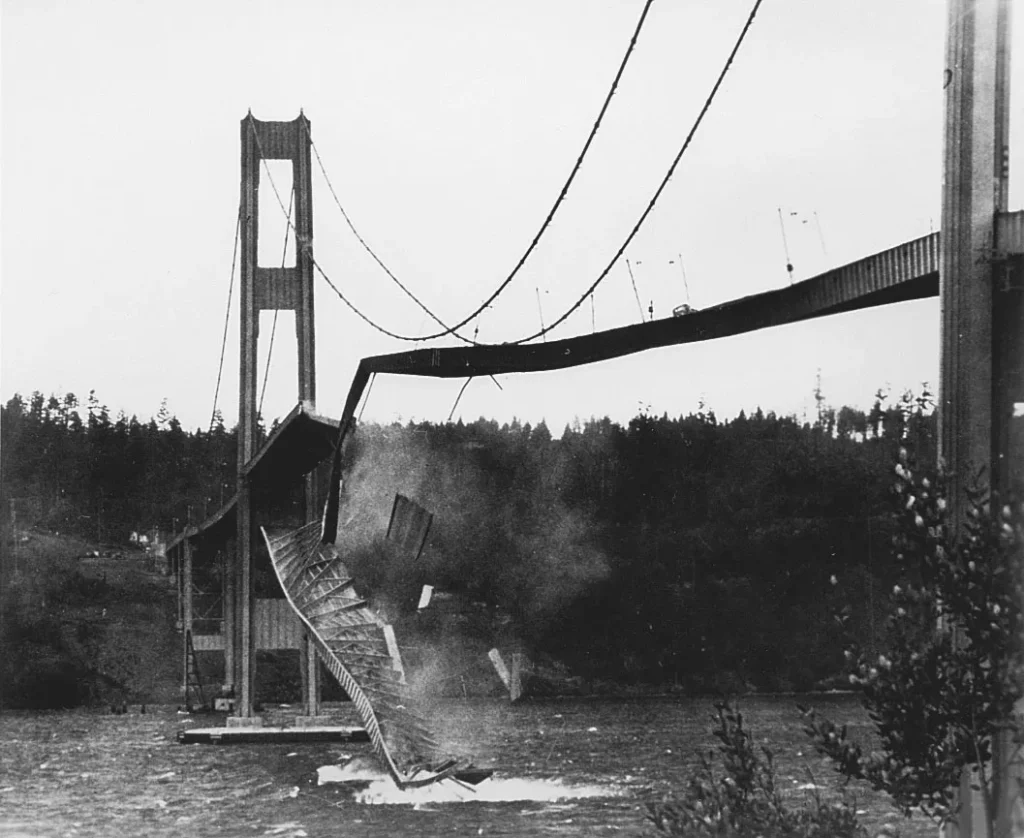
🔹 Performance Optimization – Enhancing efficiency and precision. In aerospace, vibration analysis is used to fine-tune aircraft components so they don’t vibrate excessively, ensuring smooth operation and minimizing energy loss. In Formula 1 racing, engineers use modal and harmonic analysis to optimize chassis stiffness and reduce unwanted flexing at high speeds, ensuring maximum control.

🔹 Durability and Fatigue Prevention – Reducing wear and tear over time. Structures that vibrate excessively experience material fatigue, leading to cracks, failures, and costly maintenance. Modal analysis is the first stepping stone in the process that helps to predict weak points in a design before they become a problem, extending the lifespan of bridges, engines, and industrial machinery.

🔹 Acoustic and Comfort Enhancements – Reducing noise and vibration discomfort. Ever wondered why some cars feel smoother and quieter than others? Modal analysis is also used there! Engineers analyze a vehicle’s NVH (Noise, Vibration, and Harshness) characteristics to minimize unwanted cabin vibrations and road noise.

Applications of Modal Analysis:
Modal is a critical engineering tool that ensures everything from cars to skyscrapers to jet engines can withstand the forces of nature, motion, and time. Wherever there’s movement, vibration, or structural integrity at stake, modal and harmonic analysis principles are working behind the scenes to optimize performance and prevent disasters.
🚗 Automotive Industry: The Science of a Smooth, Quiet Ride
Imagine cruising down the highway in a sleek, high-performance vehicle. You barely hear the road beneath you, the engine hums with precision, and the ride is silky smooth. In the automotive industry, modal analysis plays a crucial role in minimizing noise, vibration, and harshness (NVH)—three factors that directly impact comfort, safety, and longevity.
✅ Chassis and Body Optimization – Engineers perform modal analysis on a vehicle’s frame and body panels to identify and eliminate unwanted vibrations. This prevents irritating rattles and structural fatigue over time.
✅ Suspension Tuning – A car’s suspension system absorbs shocks and maintains stability, but if not properly tuned, it can introduce vibrations at certain speeds.
✅ Engine and Powertrain Refinement – Every engine component vibrates, and at high RPMs, even tiny resonances can become catastrophic.
👉 Real-World Example:
Electric vehicles (EVs) are designed to be ultra-quiet, but this presents a new challenge—without the masking noise of an internal combustion engine, smaller vibrations become more noticeable.

✈️ Aerospace: Keeping Aircraft Stable at 30,000 Feet
When it comes to aircraft and spacecraft, vibration control isn’t just about comfort—it’s about survival. Every component in an aircraft, from its fuselage to its wings to its engines, is subjected to extreme forces. A small miscalculation in how a structure responds to these forces can have catastrophic consequences.
✅ Flutter Prevention in Wings – Aircraft wings are long, flexible, and constantly subjected to airflow. If their natural frequency aligns with aerodynamic forces, dangerous flutter can occur, leading to structural failure.
✅ Engine Vibration Control – Jet engines operate at incredibly high speeds, and each rotating blade experiences intense vibrational forces. If resonance occurs, blade fatigue and failure can follow.
✅ Satellite and Spacecraft Durability – In space, vibrations from rocket launches and orbital maneuvers can damage delicate instruments.
⚡ Energy Sector: Powering the Future with Stability
The energy industry relies on high-speed rotating machinery, from wind turbines to power plant generators. If these components vibrate excessively, efficiency plummets, wear accelerates, and failures become inevitable.
✅ Wind Turbine Blade Optimization – Wind turbine blades must be lightweight, strong, and resistant to dynamic wind forces.
✅ Rotating Machinery Health Monitoring – Turbines, compressors, and generators operate at high speeds. If vibrations reach critical levels, they can cause bearing failures and shaft misalignment.
✅ Power Plants – Large power-generating structures experience constant vibration from turbines and water flow.
How Modal Analysis Works:
The process happens in two main stages: Modal Testing (where vibrations are physically measured) and Modal Analysis (where those measurements are processed to extract meaningful insights). Let’s take a closer look at how it all comes together.
🔨 Modal Testing: Making Structures "Sing"
Before engineers can analyze how a structure vibrates, they need to make it vibrate in a controlled way. This is called exciting the structure, and it’s done using carefully selected impact forces or continuous vibrations.
1️⃣ Exciting the Structure: The "Kick" That Starts the Vibrations
To study how a system responds to vibrations, engineers need to apply an external force—just like plucking a guitar string makes it resonate. There are two main ways to do this:
- 🔨 Impact Hammer Testing (The Quick, Direct Approach)
A specialized hammer (equipped with a force sensor) strikes the structure at a precise location.
The hammer’s built-in sensor records the exact force applied.
This method is great for quick modal tests on smaller objects like beams, panels, or mechanical components. - 🎛️Shaker Testing (The Controlled, Continuous Approach)
An electrodynamic or hydraulic shaker is attached to the structure.
The shaker vibrates the structure at a sweeping range of frequencies or at a specific, sustained frequency.
This method provides more precise control over excitation and is ideal for large structures like bridges, aircraft wings, or entire vehicle bodies.
More about it in the following video:
2️⃣ Measuring the System’s Response: How Sensors Capture Vibrations
Once the structure starts vibrating, the next step is to record how it reacts. This is done using a variety of sensors that track motion, acceleration, and deformation in real-time.
✅ Accelerometers – These tiny sensors measure acceleration at different points on the structure, revealing how different sections respond to vibration. They’re attached at key locations where engineers expect significant motion.
✅ Laser Vibrometers – A non-contact method that uses laser beams to measure vibration from a distance. Useful for delicate components or hard-to-reach areas.
✅ Strain Gauges – These sensors track deformation and stress, helping engineers see how materials stretch or compress under dynamic loads.
📊 Modal Analysis: Converting Data into Information
Once all the vibration data is collected, it’s time for the extraction of meaningful insights about how the structure vibrates:
Fourier Analysis:
Converting Raw Data Into Frequencies
Vibration signals collected from modal testing are complex waveforms, often appearing as chaotic oscillations. Engineers use Fourier analysis to break these signals down into their individual frequency components.
Fourier analysis works like taking apart a messy sound into pieces of recognizable patterns. With it the engineers can identify which frequencies are present and how strongly they contribute to the overall response. For it to make sense, an awesome video is available here about the Discrete Fourier Transformation!
💡 Example: A car’s exhaust system might generate a vibration spectrum with several peaks—each peak corresponding to a specific resonance mode that engineers need to manage for reduced cabin noise.
Extracting Modal Parameters:
Finding Natural Frequencies & Mode Shapes
Using the processed frequency data, engineers extract the modal parameters that define a structure’s vibration behavior:
✅ Natural Frequencies – The frequencies at which the structure naturally vibrates.
✅ Mode Shapes – The specific deformation patterns at each natural frequency.
✅ Damping Ratios – How quickly vibrations dissipate over time.
Experimental vs. Analytical Modal Analysis: Testing vs. Simulating
When it comes to understanding the vibration characteristics of a structure, engineers rely on two main approaches:
- Experimental Modal Analysis (EMA): Physically testing a real-world object to measure its vibrations.
- Analytical Modal Analysis (FEA-based): Using computer simulations, like Finite Element Analysis (FEA), to predict vibrational behavior before an object is built.
- The Hybrid Approach: Combining physical tests and simulations for the highest accuracy.
Each method has its strengths, weaknesses, and ideal use cases. Let’s break them down.
When it comes to understanding the vibration characteristics of a structure, engineers rely on two main approaches:
- Experimental Modal Analysis (EMA): Physically testing a real-world object to measure its vibrations.
- Analytical Modal Analysis (FEA-based): Using computer simulations, like Finite Element Analysis (FEA), to predict vibrational behavior before an object is built.
- The Hybrid Approach: Combining physical tests and simulations for the highest accuracy.
Each method has its strengths, weaknesses, and ideal use cases. Let’s break them down.
🔬 Experimental Modal Analysis (EMA): Measuring
💡 “Let’s hit it and see what happens.”
Experimental Modal Analysis (EMA) is the hands-on approach to modal testing. Instead of relying on theoretical models, engineers use real structures, real forces, and real measurements to determine how an object vibrates.

-A structure is excited using impact hammers or shakers.
–Sensors (accelerometers, laser vibrometers) capture the response.
–Data acquisition systems record the vibrations.
-Engineers process the data to extract natural frequencies, mode shapes, and damping ratios.
This method is invaluable because it measures the actual physical behavior of a structure, accounting for real-world imperfections like:
- Manufacturing variations (no two objects are exactly the same).
- Material inconsistencies (real materials behave differently than theoretical ones).
- Environmental effects (temperature, humidity, wear-and-tear).
When EMA is Used:
✅ Existing structures or prototypes – Bridges, aircraft wings, car chassis, turbines.
✅ Quality control – Verifying that manufactured products match design specs.
✅ Real-world troubleshooting – Diagnosing vibrations, cracks, or fatigue failures.
Limitations of EMA:
❌ Requires physical access – Can’t test something that doesn’t exist yet.
❌ Time-consuming & expensive – Setting up and conducting tests takes effort.
❌ Limited test conditions – Hard to simulate extreme environments (space, deep-sea, high-speed airflow).
🖥️ Analytical Modal Analysis (FEA-Based): The Power of Simulation
💡 “What if we could predict the vibrations before even building the structure?”
Analytical modal analysis uses computer simulations to calculate how a structure will vibrate—long before it’s physically built. This is done using Finite Element Analysis (FEA), a computational technique that breaks a complex object into smaller elements and solves the equations of motion for each.
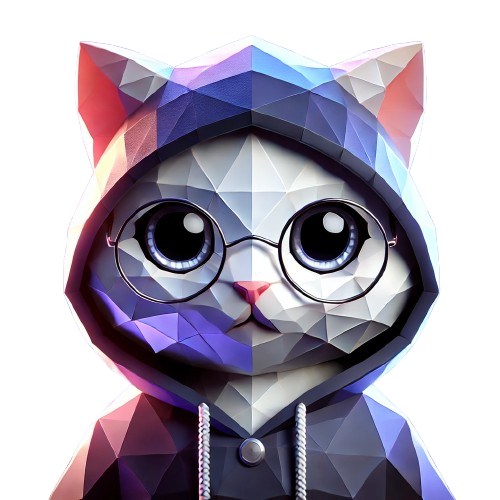
-A 3D model of the structure is created in FEA software.
-The model is divided into a finite element mesh (thousands or millions of small interconnected elements).
-Engineers assign material properties (density, stiffness, damping).
-The software solves for natural frequencies and mode shapes using mathematical eigenvalue analysis.
-The results are visualized—engineers see how the structure deforms at different frequencies.
This approach is invaluable because it allows engineers to analyze, iterate, and refine designs before manufacturing even begins.
When FEA-Based Modal Analysis is Used:
✅ Early-stage design – Testing multiple designs before choosing the best.
✅ High-cost structures – Aerospace, automotive, and civil engineering projects where prototypes are expensive.
✅ Extreme environments – Simulating earthquakes, high-speed airflow, space vacuum conditions, etc.
Limitations of Analytical Modal Analysis:
❌ Relies on accurate material data – If material properties aren’t precise, results can be misleading.
❌ Boundary conditions matter – A small modeling error (like assuming a fixed support when it’s actually flexible) can throw off the results.
❌ Still needs validation – No simulation is perfect; real-world testing is required to confirm accuracy.
Factor | Experimental Modal Analysis (EMA) | Analytical Modal Analysis (FEA) |
---|---|---|
Used When? | Existing physical structures | Early-stage design, no prototype needed |
Pros | Real-world accuracy, includes manufacturing effects | Fast, cost-effective, allows design iteration |
Cons | Time-consuming, expensive | Results depend on model accuracy |
Best For? | Troubleshooting, validation, quality control | Design optimization, pre-production testing |
Overall Strength | Measures actual behavior | Predicts before manufacturing |
Conclusion:
Modal analysis is a fundamental tool in modern engineering, providing critical insights into the dynamic behavior of structures. By identifying natural frequencies, mode shapes, and damping properties, engineers can predict potential failures, enhance performance, and design structures that withstand real-world conditions.
Across industries—from automotive and aerospace to civil engineering and energy production—modal analysis plays a key role in ensuring safety, durability, and efficiency. Whether through experimental testing or computational simulations, it allows for data-driven decision-making, reducing risks and optimizing performance before a product ever reaches production.
Looking Forward
As technology advances, the applications of modal analysis continue to expand. With the growing capabilities of Finite Element Analysis (FEA), real-time structural health monitoring, and AI-driven predictive modeling, engineers are equipped with more powerful tools than ever to refine designs and push the boundaries of innovation.
For professionals and students alike, a deeper understanding of modal analysis opens doors to more precise engineering solutions. Whether through hands-on experimentation or digital simulations, exploring the principles of structural dynamics is a step toward designing a more stable, efficient, and resilient world.
What is Modal Analysis?
© Copyright 2025 - All Rights Reserved